The world of industrial production has seen remarkable advancements, particularly in the realm of canister filling machines. These devices, integral to the packaging and distribution sectors, have evolved significantly, underpinned by enhanced precision, efficiency, and technological innovations. In this piece, we delve into the intricacies of canister filling machines, offering insights based on comprehensive industry experience, professional expertise, authoritative insights, and verifiable trustworthiness.
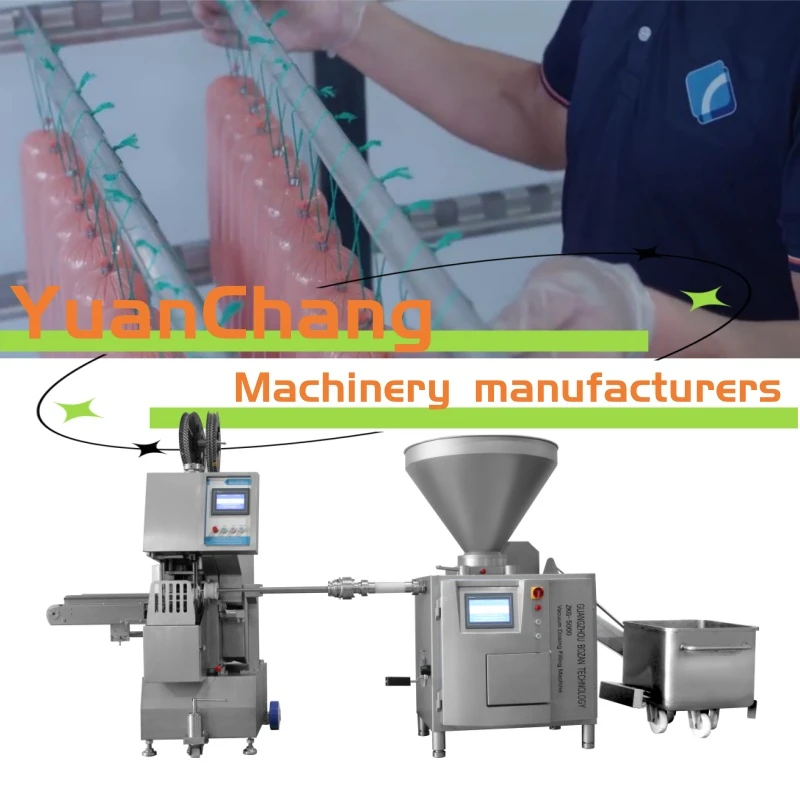
Canister filling machines are paramount in ensuring product consistency, quality control, and operational efficiency. They are engineered to streamline the process of filling canisters with various products, including liquids, aerosols, and powders. These machines are pivotal in industries ranging from pharmaceuticals and cosmetics to food and chemical manufacturing. The operational efficiency of these machines significantly reduces wastage and ensures that product measurements are accurate to the highest standards, which is crucial for maintaining product integrity.
From an experience standpoint, canister filling machines have demonstrated remarkable versatility across numerous applications. The capacity to handle a wide range of viscosities and container sizes without compromising speed or accuracy speaks volumes about their engineering sophistication. Manufacturing professionals emphasize the importance of regular maintenance and calibration of these machines to ensure continued optimal performance. Neglecting these practices can lead to decreased efficiency and potential product variability, underscoring the need for vigilant operational protocols.
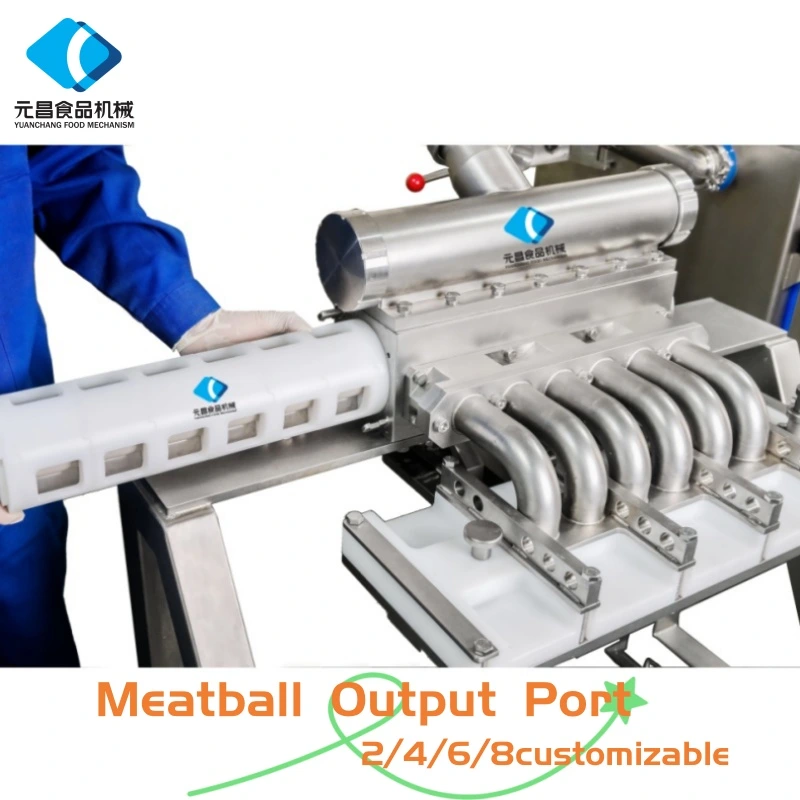
Expertise in canister filling machines encompasses understanding the delicate balance between speed and precision. During the filling process, these machines must handle high throughput rates while maintaining consistent fill levels. This requires not only advanced sensor technologies but also precise control mechanisms. Industry experts often recommend adopting systems with automated features, which simplify the monitoring process and enhance the machine's responsiveness to variabilities in product flow. The adoption of AI and machine learning algorithms in these systems is a cutting-edge trend that further bolsters their operational capabilities by predicting and mitigating potential filling inconsistencies.
canister filling machine
In terms of authoritativeness, canister filling machines are supported by a robust regulatory framework that ensures compliance with industry standards. Adherence to standards such as the ISO and GMP is mandatory, highlighting the importance of maintaining product safety and integrity in highly regulated sectors like pharmaceuticals and food production. These standards not only safeguard consumers but also instill confidence in manufacturers who rely on consistent and compliant packaging solutions.
Trustworthiness in the domain of canister filling machines is consolidated through rigorous testing and quality assurance processes. Manufacturers and users alike invest in extensive testing to ensure the machines' reliability under various operational conditions. The choice of materials in these machines, often stainless steel for its durability and chemical resistance, further reinforces trust in the device's capability to handle diverse product types without contamination risks.
In conclusion, canister filling machines represent the pinnacle of modern packaging technology. Their ability to deliver accuracy, reliability, and efficiency is backed by accumulated industry experience, profound expertise, and strict adherence to authoritative standards. Trust is woven into every component of their design and operation, making them indispensable assets in sectors that demand precision and quality. As industries continue to evolve, the role of canister filling machines is set to expand, driving forward innovations that enhance production capabilities and uphold the highest standards of quality and safety.