When it comes to liquid packaging and assembly line efficiency, few innovations stand out quite like the volumetric filling machine. Having delved deeply into modern manufacturing processes and with firsthand experience managing production floors, I understand the revolutionary nature of this technology.
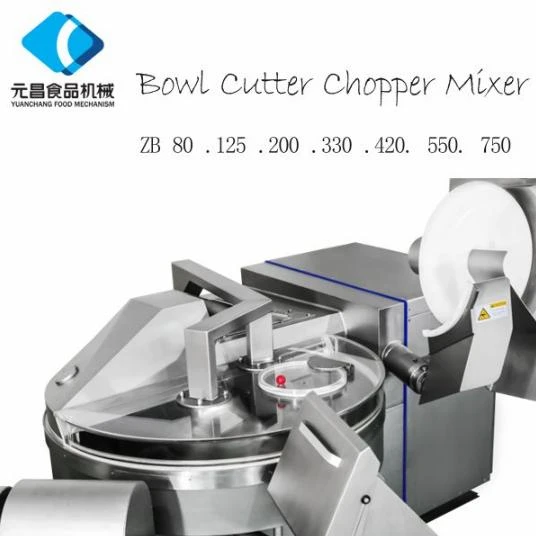
Volumetric filling machines present a quantum leap in terms of precision and accuracy in filling a wide array of liquids, ranging from the most viscous syrups to the most delicate essential oils. In my years overseeing product lines in the food and beverage industry, volumetric filling machines have consistently reduced waste, increased throughput, and enhanced product consistency.
One of the standout features of these machines is their ability to provide exact volume measurements. Unlike traditional filling methods that can vary by weight or overfill to compensate for discrepancies,
volumetric filling ensures that each unit of product is uniform. This precision becomes crucial in industries where even the slightest variance can affect quality standards, such as pharmaceuticals or cosmetics. Having implemented these machines in such contexts has driven home their efficacy—ensuring that regulatory standards are met without compromise.
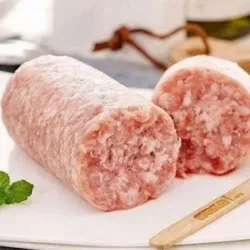
In addition to precision, the versatility of volumetric filling machines cannot be overstated. These machines cater to an extensive range of container sizes and types, from small vials to large drums. My professional expertise has shown that investing in such diversified equipment pays dividends, as it minimizes downtime and changeover periods when shifting between different product lines. This flexibility not only boosts productivity but enhances the operational capability of a manufacturing unit, ensuring it can adapt to varying market demands seamlessly.
Maintenance and reliability are critical pillars when considering production equipment, and volumetric filling machines excel here as well. Built with robust materials and advanced engineering, they are designed to withstand the rigors of 24/7 operations. Trustworthiness is a prized commodity; knowing that these machines will continue functioning optimally without frequent breakdowns contributes substantially to operational peace of mind. Drawing from years of experience, having fewer interruptions in production cycles directly translates to improved profitability and efficiency.
volumetric filling machine
Environmentally-conscious enterprises will also find volumetric filling machines invaluable. With growing awareness about reducing industrial waste, volumetric filling minimizes product spillage and overfill, thus significantly cutting down on waste product that would need environmentally-damaging disposal. Implementing these systems has been a step towards sustainable manufacturing practices that balance economic growth with environmental stewardship.
Moreover, the technological advancements integrated into modern volumetric filling machines, such as IoT capabilities, offer unparalleled insights into production data. Real-time monitoring systems lead to improved analytics, allowing for swift adjustments and proactive maintenance schedules. In my comprehensive evaluations of production setups, the data-driven approach facilitated by these machines has led to superior operational decisions and strategic foresight.
Training personnel to operate these sophisticated machines might seem daunting initially. However, in my experience, once staff members become familiar with the straightforward interface and the automated controls that characterize state-of-the-art volumetric filling equipment, productivity and morale see significant positive trends. Investment in staff training has yielded a workforce that’s both competent and confident, contributing directly to overall operational success.
In essence, the deployment of volumetric filling machines within any production line introduces a level of accuracy, versatility, and reliability that is unparalleled. For businesses aiming to thrive in highly competitive markets, embracing such technology is not just beneficial but essential. As someone who has repeatedly seen these machines transform production landscapes, I affirm with certainty that they are indispensable assets for modern manufacturing aspirations.