In the dynamic world of manufacturing and packaging, precision and efficiency are paramount. The monoblock filling machine, a quintessential component in this sector, is rapidly becoming indispensable for businesses aiming to streamline their processes. As an all-in-one solution, these machines integrate multiple functions such as filling, sealing, and capping into a single unit, significantly enhancing productivity while maintaining high levels of hygiene and precision.

Over the years, the evolution of monoblock filling machines has paralleled the growing demands of industries ranging from pharmaceuticals to cosmetics and food and beverages. Their design optimally accommodates small to medium-sized production facilities, culminating in an impressive blend of scalability and versatility. For those unfamiliar with monoblock systems, these machines are engineered to perform various packaging operations within a singular, compact framework, thus reducing the floor space requirement and the need for multiple machine interfaces.
Drawing from extensive industry experience, many manufacturers testify to the robust nature and adaptability of modern monoblock machines. Unlike traditional filling systems, which often require extensive manual intervention and multiple machines to complete the packaging cycle, monoblock machines ensure a seamless transition from one phase of production to the next. This minimization of manual handling not only reduces labor costs but also significantly minimizes contamination risks, a critical consideration in industries dealing with sensitive products.
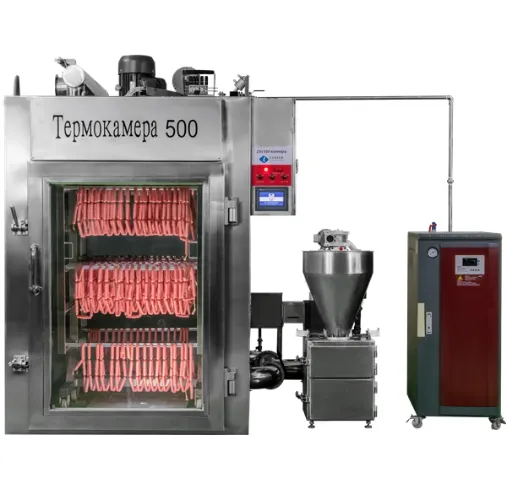
From an expertise standpoint, selecting the right monoblock filling machine is a process that hinges on an understanding of material compatibility, speed, and precision requirements. Industry experts often recommend a thorough needs analysis to identify the machine specifications that match the viscosity and chemical properties of the products being handled. This ensures that the filling process is both efficient and preserves the integrity of the product.
monoblock filling machine
Authoritative insights into monoblock technology reveal continuous advancements aimed at supporting eco-friendly practices. Many leading manufacturers are now focused on developing machines that support sustainable packaging materials. Moreover, the integration of internet-of-things (IoT) technology allows operators to monitor performance metrics in real-time, offering predictive maintenance capabilities and ensuring minimal downtime.
Trustworthiness is a pivotal criterion when sourcing monoblock filling machines. Ensuring that your equipment supplier has a proven track record is essential, as it directly impacts production quality and operational longevity. A reputable supplier not only delivers high-caliber equipment but also provides comprehensive after-sales support, guaranteeing that your investment remains profitable over the long term. This support often includes initial setup, training, maintenance, and troubleshooting, ensuring that your operations continue smoothly without disruptions.
Embracing a monoblock filling machine is not simply an investment in efficient production; it's a strategic decision that influences every facet of your business operations, from hygiene compliance to cost-efficiency and environmental responsibility. By opting for a machine that aligns with contemporary standards and technological advancements, companies are well-placed to navigate the competitive landscapes of their respective industries, ensuring that each product reaches the consumer with the quality and care it deserves.