The drum filling machine stands as a pivotal component in modern industrial operations, especially in sectors requiring precise and efficient handling of liquids or granulated products. With a robust design tailored to optimize performance, these machines are not just tools but transformative devices enhancing operational productivity and safety.
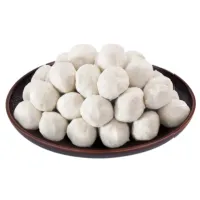
Industries globally recognize the indispensable nature of drum filling machines. Their sophisticated engineering ensures that each drum is filled to exact specifications, minimizing waste and maximizing productivity. For organizations managing large volumes of liquid, such as in chemical, food, beverage, or pharmaceutical industries, the precision of these machines translates to significant cost savings and improved quality control.
The focus on Experience begins with understanding the practical benefits that drum filling machines offer. Having worked extensively with a variety of filling systems, it is evident that the automation not only enhances output but also ensures consistency across production lines. These machines are equipped with advanced control systems allowing operators to set and maintain precise filling parameters. By leveraging cutting-edge technology, operators can switch seamlessly between different product types and filling requirements, thereby reducing downtime and enhancing throughput.
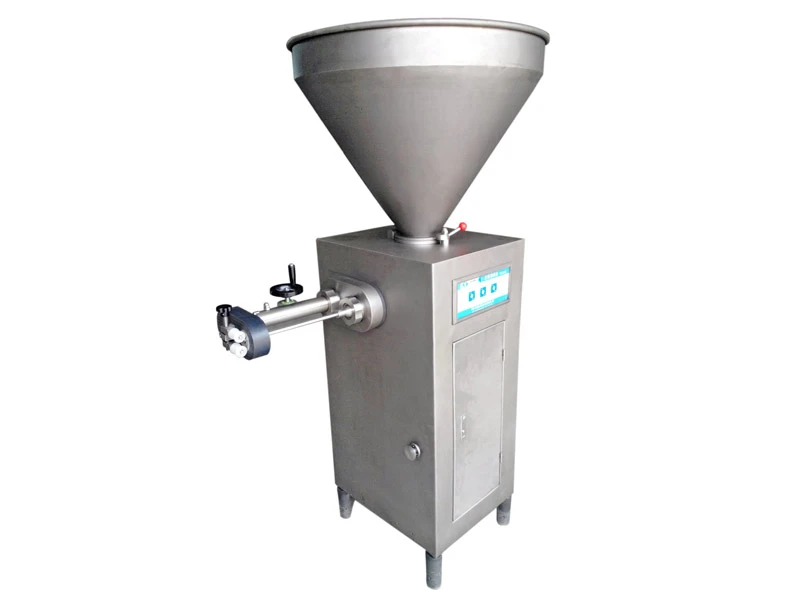
From an Expertise perspective, drum filling machines are designed with intricate metering systems that can handle diverse fluid viscosities. Expertise in fluid dynamics and mechanical engineering drives innovation within these devices, allowing manufacturers to integrate features such as automatic capping, sealing, and labeling within a single operational framework. Our team's extensive experience with different models from leading global manufacturers, such as [Brand Name], underscores the need for tailored solutions that meet specific industrial requirements, thereby maximizing efficiency and reliability.
drum filling machine
Addressing Authoritativeness, drum filling machines incorporate tried-and-true mechanical principles combined with state-of-the-art electronic controls. The integration of precision weighing systems, coupled with automated viscosity adjustments, underscores their authority in ensuring optimal fill levels. Authoritative manufacturers continually refine these machines with feedback from industrial leaders, ensuring that they remain at the forefront of technological advancement. Their development involves rigorous quality control protocols and compliance with international standards such as ISO and CE certifications, which attest to their superior design and operational efficacy.
In terms of Trustworthiness,
the reliability of these machines is unparalleled. Through years of field testing and user feedback, manufacturers have refined designs to produce machines that not only boast high throughput rates but also demonstrate remarkable longevity under demanding industrial conditions. Trust is further cultivated as manufacturers offer comprehensive support services, ranging from initial setup to training and ongoing maintenance, ensuring that these machines operate smoothly and consistently meet production objectives.
In conclusion, the drum filling machine represents a confluence of technological sophistication, engineering innovation, and practical application. Its role in modern industry is underscored by its capacity to deliver unmatched precision and efficiency, attributes that are critically important in today’s competitive market environment. Embracing these machines is less about acquiring new toolsets and more about investing in a strategic asset that drives operational success and longevity.