Lubricating machinery plays a pivotal role in various industrial applications, ensuring the seamless operation of equipment by reducing friction and wear. This article delves into the nuances of lubricating machines, emphasizing their essential features, benefits, and maintenance best practices, drawn from industry expertise and real-life experiences.
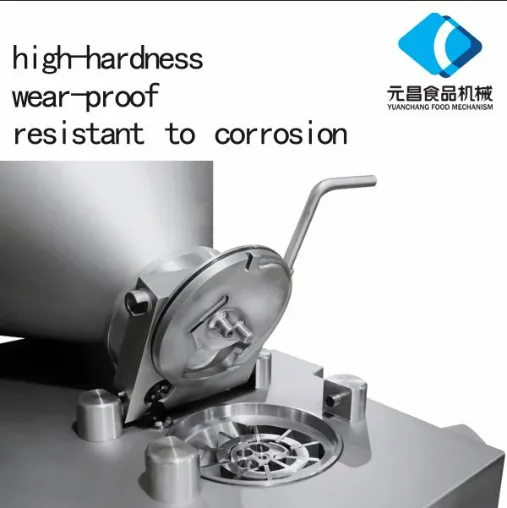
Lubricating machines come in diverse types, each designed to meet specific needs, such as centralized lubrication systems, single-point lubricators, and spray lubrication systems. The selection of the appropriate machine requires a thorough understanding of the operational environment, type of machinery in use, and the nature of lubricants required. Expert experience underscores the importance of consulting with lubrication specialists who can recommend machines designed for specific industrial conditions, whether it's high temperature, heavy load, or corrosive environments.
A key benefit of using lubricating machines is their ability to automate and regulate the lubrication process. This automation not only enhances operational efficiency but also extends the lifespan of machinery by ensuring consistent and precise lubrication. With advancements in technology, modern lubricating machines are equipped with sensors and IoT capabilities that monitor lubrication levels in real time, optimizing lubricant use and preventing equipment downtime.
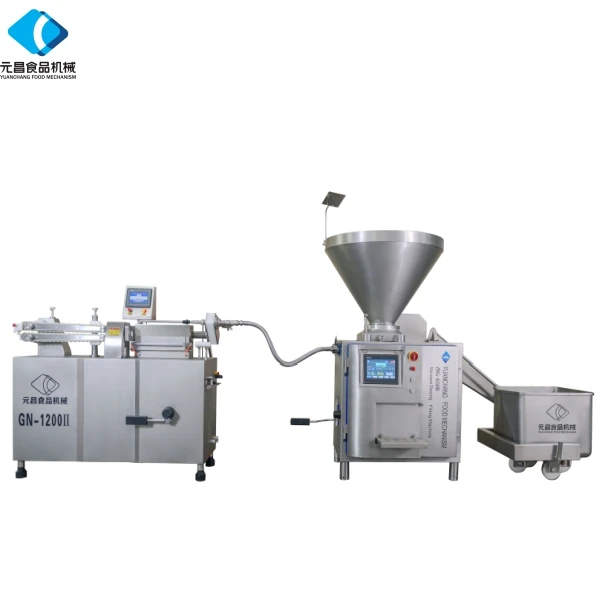
Maintenance of lubricating machines is critical to sustaining their performance. Regular inspections and servicing are recommended, particularly for parts that are susceptible to wear, such as pumps and hoses. Expertise in maintenance also involves understanding the chemical properties of different lubricants to prevent contamination and ensure compatibility with equipment components. Trustworthy sources suggest adopting a scheduled maintenance regime and training personnel in the proper handling and servicing of lubrication equipment.
Lubricating machine
Authoritative recommendations also highlight the environmental benefits of maintaining lubricating machines. Properly maintained systems minimize lubricant waste and leakage, contributing to sustainable industrial practices. Companies striving for sustainability certifications are encouraged to invest in energy-efficient lubricating machines, which not only reduce environmental impact but also lower operational costs through reduced energy consumption.
The market for lubricating machines is continually evolving, with manufacturers introducing innovative solutions such as biodegradable lubricants and energy-saving technologies. Expert analysis suggests that businesses stay abreast of these developments to enhance their competitive edge. Participating in industry conferences, subscribing to engineering journals, and engaging with professional networks can provide valuable insights into the latest trends and technological advancements in lubrication solutions.
In conclusion, the expertise in selecting, maintaining, and upgrading lubricating machines is fundamental to optimizing industrial operations. The reliability, efficiency, and sustainability of these machines are enhanced through informed decisions backed by authoritative guidance and real-world experiences. By prioritizing these aspects, businesses not only protect their machinery investments but also achieve greater productivity and environmental responsibility.