In the bustling world of beverage production, efficiency and precision play pivotal roles in ensuring a successful operation. Equipment designed for bottling is at the heart of this industry—an indispensable component that substantially influences the quality and speed of production. This article delves into the intricacies of bottling equipment, offering a unique insight drawn from several years of hands-on experience with some of the most trusted brands in the market.
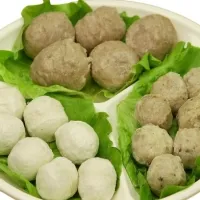
The dynamic nature of bottling operations necessitates equipment that balances speed with accuracy. Advanced bottling machines are engineered to handle a plethora of liquids, ranging from water to complex carbonated drinks, with precision that guarantees the integrity of the product. Through the utilization of state-of-the-art technology, these machines optimize production by minimizing waste and ensuring consistent fill levels. This precision not only enhances product quality but significantly boosts operational efficiency.
Drawing from extensive expertise, certain features stand out as critical in the selection of bottling equipment.
Automation is a cornerstone of modern bottling processes. Cutting-edge equipment features programmable logic controllers (PLCs) and human-machine interfaces (HMIs) that provide unparalleled control over the entire bottling line. This allows operators to easily modify production speeds, change bottle sizes, and adjust fill levels, ensuring seamless operations even in high-demand scenarios.
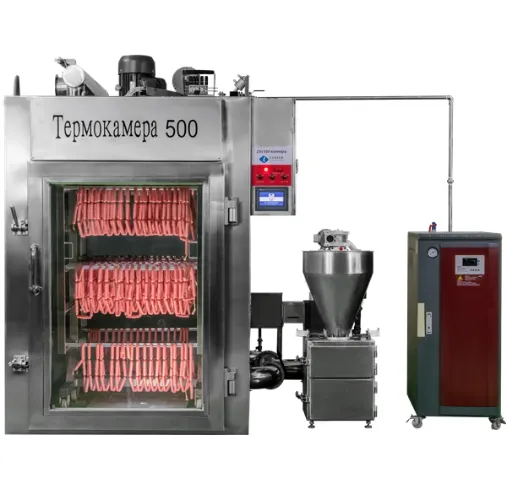
The type of bottling equipment should align with the specific needs of a production facility. Rotary fillers, for instance, are ideal for high-volume operations due to their high-speed capabilities and small footprint. Conversely, inline fillers are perfect for smaller operations that require more flexibility with their bottling processes. The right choice depends on the scale of operations and the variety of products being bottled.
Equipment for pouring
When considering investment in bottling equipment, it’s essential to emphasize durability and maintenance. Equipment crafted from high-quality stainless steel offers excellent resistance to corrosion and wear, ensuring longevity even in rigorous production environments. Regular maintenance, facilitated by easy access to machine components, minimizes downtime and prolongs the lifespan of the equipment. Established brands often provide comprehensive support and training, enhancing the competence and confidence of the bottling line operators.
The importance of compliance with health and safety standards cannot be overstated. Reliable bottling equipment adheres to stringent food safety regulations, safeguarding both the product and the consumer. Equipment featuring CIP (Clean-In-Place) systems offers a noteworthy advantage by allowing complete cleaning without disassembly, thereby reducing contamination risks and maintaining high hygiene standards.
Trust in bottling equipment is forged through a consistent track record of performance and reliability. Brands that have established themselves in the industry often back their equipment with extensive warranties and responsive customer service. These manufacturers usually provide detailed documentation and resources, empowering users to optimize their operations and quickly address any technical issues that may arise.
In conclusion, the strategic selection and use of bottling equipment profoundly impact the success of beverage production operations. By leveraging advanced technology, ensuring rigorous adherence to safety standards, and cultivating a robust support system, companies can enhance their efficiency, produce high-quality products, and establish enduring trust with their customers. This nuanced understanding, born from years of practical experience, solidifies the role of bottling equipment as a cornerstone of the beverage industry’s future.