Industrial thermal chambers have become indispensable tools across numerous sectors, from aerospace to pharmaceuticals, due to their ability to simulate varied environmental conditions. These chambers are not mere boxes with temperature controls; they combine high-level engineering with precise computational algorithms to create ultra-stable conditions for testing. This article delves into why these devices stand at the pinnacle of product testing and how businesses leverage their capabilities for optimal results.
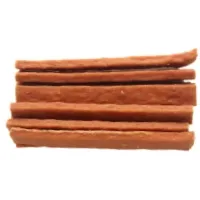
Industrial thermal chambers are revered for their versatility. Capable of replicating a wide range of temperatures and humidity levels, they offer crucial insights into a product's durability and performance. Industries such as automotive and electronics heavily rely on these chambers to ensure their products can withstand extreme conditions, from arctic cold to desert heat. The expertise behind designing these chambers makes them robust and efficient, creating a controlled environment that replicates the harshest weather conditions on the planet.
One of the most profound experiences shared by engineers using industrial thermal chambers is their ability to predict product life cycles accurately. Understanding how a product responds to environmental stressors helps manufacturers enhance product durability, thus reducing recalls and boosting consumer trust. This predictability is a testament to the expertise invested in developing the specific algorithms and control systems that govern these chambers.
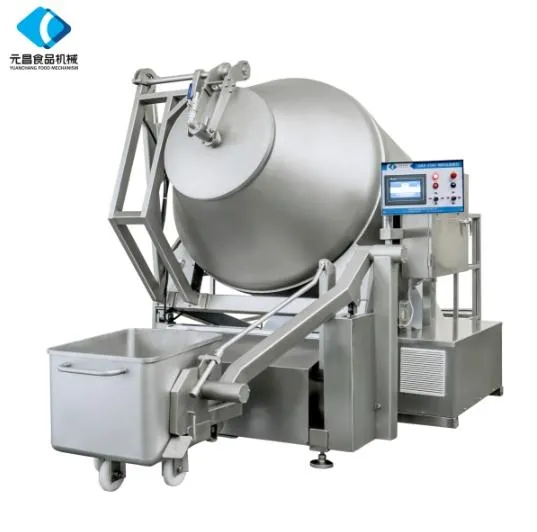
Further elevating their authority in product testing, certain thermal chambers are equipped with advanced climatic conditioning capabilities. The inclusion of rapid temperature cycling and humidity control allows these chambers to test for thermal shock—a scenario where items endure rapid temperature changes that might lead to structural failure. The chambers' authority stems from their consistent performance in such demanding tests, validating product resilience before market release.
Industrial thermal camera
Trustworthiness is another hallmark of industrial thermal chambers. The data generated during testing is precise and reproducible, crucial for maintaining integrity in scientific research and technical validation. Given their pivotal role, thermal chambers often adhere to stringent international standards like ISO and ASTM. This compliance not only ensures trust in the results produced but also supports businesses in meeting international market requirements.
From an experiential standpoint, the automation and integration capabilities of modern thermal chambers represent a significant advancement. Technicians can now program and monitor tests remotely, integrating these chambers with IoT systems for real-time data acquisition and analysis. Such innovations increase the efficiency of testing processes, enabling engineers to make instant adjustments and improvements based on live data. These chambers are not confined to past paradigms of manual control but are sophisticated, user-friendly devices molded by years of technological refinement.
Industries are increasingly turning to thermal chambers as indispensable tools for quality assurance. Their ability to simulate precise climatic conditions and deliver reliable data underscores their pivotal role in modern manufacturing and research. The blend of cutting-edge technology and detailed craftsmanship ensures these chambers not only meet current industrial demands but also anticipate future needs.
In conclusion, the value of industrial thermal chambers lies in their precision, adaptability, and reliability. The expertise invested in their design and the rigorous standards they meet affirm their significant position in product testing and development. By continuing to evolve, these chambers remain integral to businesses seeking to fortify their market presence through durable, high-quality products.